Non-Electrospinning STEP Platform
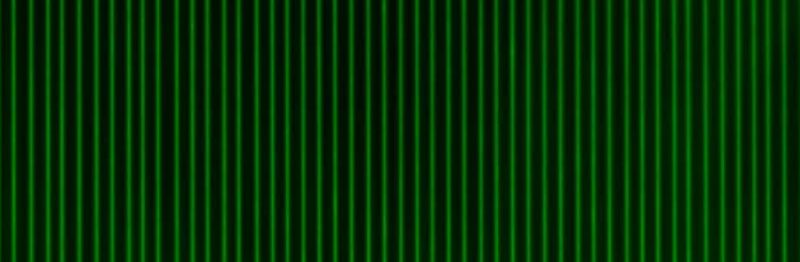
Nanofibers are one of the most intriguing 1D building blocks with unique properties. Nanofibers are being increasingly used in a variety of applications including biomedical, materials, electronics, etc. Numerous techniques exist to-date that are able to fabricate these high aspect ratio (length/diameter) fibers.
Fabrication Method | Major mechanism of fiber fabrication | Diameter range of fibers | Characteristics/Advantages | Disadvantages |
---|---|---|---|---|
Conventional electrospinning | Electric field (~ 10-30kV) | <50-10,000 nm | Mass production of fibers spun from a wide range of polymers. | Presence of a high voltage electric source results in poor alignment of fibers and wide spread in fiber diameters |
Near field electrospinning (NFES) | Electric field (~ 0.2-1.8kV) | 50-2500nm | Aligned fibers as compared to conventional electrospinning due to lower electric fields & source-to-target distances involved | Low output compared to conventional electrospinning processes, short source-to-target distance hampers fiber solidification |
Direct write melt electrospinning | Electric field coupled with high temperature | 10-40 µm | Aligned fiber networks from a wide range of polymers | Very large fiber diameters (~20 µm), thus essentially microfibers, not suitable for mimicking native ECM |
Rotary jet spinning | Centrifugal force (up to 75,000 RPM) | 425-1600 nm | High throughput of fiber production from a wide range of polymers. | Poor control in fiber diameter and restricted to only uniaxial arrays within a ring-shaped fiber construct |
Pull spinning | Axial/Rotational stretch (up to 45,000 RPM) | 200-1500 nm | Portable setup and sufficiently high throughput of aligned nanofibers | Poor control over fiber spacing |
Spinneret based Tunable Engineered Parameters (STEP) | Pseudo dry spinning | <50-10,000 nm | Aligned nanofibers with precisely tunable diameter, spacing and orientation. | Repeatable production of large diameter (>10 µm) fibers has not yet been investigated using the current version of STEP. |
Our Non-electrospinning Approach
We have pioneered Spinneret based Tunable Engineered Parameters (STEP, US Patents 990293, 9029149 and 9,753,023), which does not require an electrical source during fiber fabrication. Elimination of the electrical source overcomes notable shortcomings of electrospinning method and provides control on fiber diameter, spacing, orientation and architecture. Using customizable fiber architectures, we study mechanobiology, develop advanced materials and methods to characterize individual, multiple and bundles of fibers. In collaboration with Behkam lab, we have pioneered Spun-wrapped Aligned Nanofiber (SWAN) lithography process for permanent features on 3D objects of different shapes and sizes.
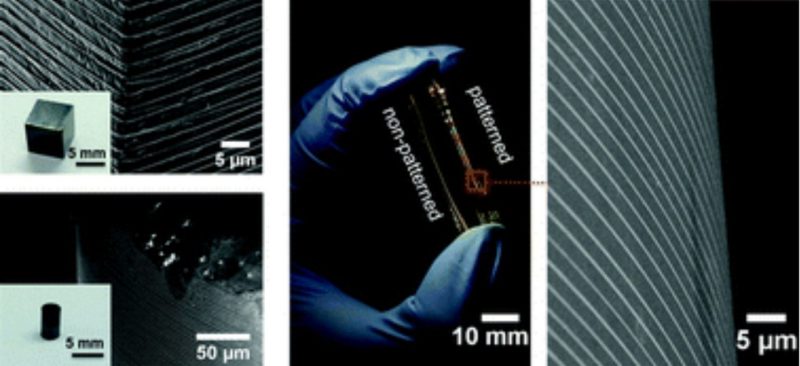
Fabrication of micro/nano-structures on irregularly shaped substrates and three-dimensional (3D) objects is of significant interest in diverse technological fields. However, it remains a formidable challenge thwarted by limited adaptability of the state-of-the-art nanolithography techniques for nanofabrication on non-planar surfaces. In this work, we introduce Spun-Wrapped Aligned Nanofiber (SWAN) lithography, a versatile, scalable, and cost-effective technique for fabrication of multiscale (nano to microscale) structures on 3D objects without restriction on substrate material and geometry. SWAN lithography combines precise deposition of polymeric nanofiber masks, in aligned single or multilayer configurations, with well-controlled solvent vapor treatment and etching processes to enable high throughput (>10−7 m2 s−1) and large-area fabrication of sub-50 nm to several micron features with high pattern fidelity. Using this technique, we demonstrate whole-surface nanopatterning of bulk and thin film surfaces of cubes, cylinders, and hyperbola-shaped objects that would be difficult, if not impossible to achieve with existing methods. We demonstrate that the fabricated feature size (b) scales with the fiber mask diameter (D) as b1.5 ∝ D. This scaling law is in excellent agreement with theoretical predictions using the Johnson, Kendall, and Roberts (JKR) contact theory, thus providing a rational design framework for fabrication of systems and devices that require precisely designed multiscale features.
Study led by Behkam Lab, Virginia Tech
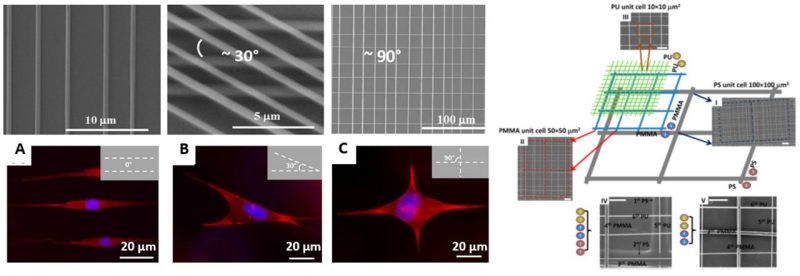
Extracellular matrix (ECM) is a fibrous natural cell environment, possessing complicated micro- and nanoarchitectures, which provide extracellular signaling cues and influence cell behaviors. Mimicking this three-dimensional microenvironment in vitro is a challenge in developmental and disease biology. Here, suspended multilayer hierarchical nanofiber assemblies (diameter from micrometers to less than 100 nm) with accurately controlled fiber orientation and spacing are demonstrated as biological scaffolds fabricated using the non-electrospinning STEP (Spinneret based Tunable Engineered Parameter) fiber manufacturing technique. Micro/nanofiber arrays were manufactured with high parallelism (relative angles between fibers were maintained less than 6°) and well controlled interfiber spacing (<15%). Using these controls, we demonstrate a bottom up hierarchical assembly of suspended six layer structures of progressively reduced diameters and spacing from several polymer systems. We then demonstrate use of STEP scaffolds to study single and multicell arrangement at high magnifications. Specifically, using double layer divergent (0°–90°) suspended nanofibers assemblies, we show precise quantitative control of cell geometry (change in shape index from 0.15 to 0.57 at similar cell areas), and through design of scaffold porosity (80 × 80 μm2 to 5 × 5 μm2) quadruple the cell attachment density. Furthermore, using unidirectional or crisscross patterns of sparse and dense fiber arrays, we are able to control the cell spread area from ∼400 to ∼700 μm2, while the nucleus shape index increases from 0.75 to 0.99 with cells nearly doubling their focal adhesion cluster lengths (∼15 μm) on widely spaced nanofiber arrays. The platform developed in this study allows a wide parametric investigation of biophysical cues which influence cell behaviors with implications in tissue engineering, developmental biology, and disease biology.
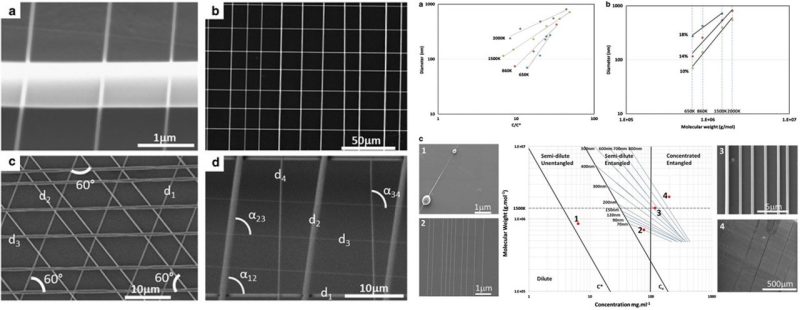
Polymeric micro/nanofibers are increasingly gaining importance due to their versatile applications in diverse fields, such as tissue engineering, smart textiles, sensors and actuators. Traditionally, the well-established techniques of spun bounding, melt blowing, dry spinning, conjugate spinning and CO2 laser thinning produce polymeric fibers with diameters on the micron scale and lengths in excess of a meter. However, aligned deposition and continuous production of long fibers with nanoscale diameters has been a challenge due to the fragility of polymeric materials. An isodiametric design space is developed to deposit PS fibers with diameters ranging from 70 to 800 nm with lengths of at least several millimeters. Molecular entanglement-based scaling laws are used to investigate the role of polymer chain entanglements on fiber formation and to demonstrate that smooth, uniform fibers of substantial length are obtained at concentrations approaching and exceeding the critical entangled concentration (Ce). Visual inspection of the isodiametric design space provides knowledge of the polymer molecular weight and solution concentration rheology required to fabricate continuous high aspect ratio fibers.
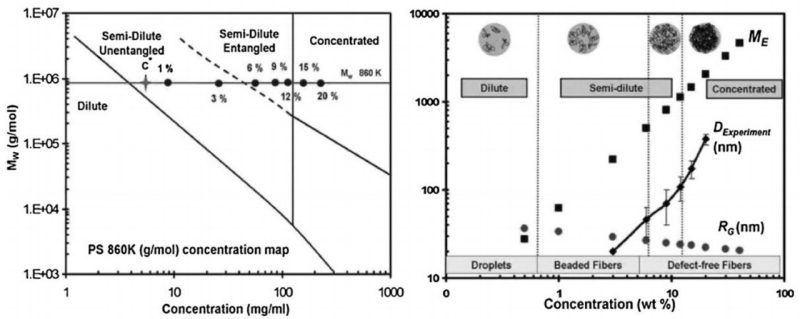
Polymeric nanofibers are finding increasing number of applications and hold the potential to revolutionize diverse fields such as tissue engineering, smart textiles, sensors, and actuators. Aligning and producing high aspect ratio fiber arrays (length/diameter > 2 000) in the submicron and nanoscale diameters has been challenging due to fragility of polymeric materials, thus making it difficult to deposit them as one dimensional structures functionally interfaced with other systems. Here, we present a pseudo dry spinning technique which allows precise control on fiber diameters and further allows deposition of fiber arrays in aligned configurations. Control on fiber diameters ranging from 50–500 nm and having lengths of several millimeters is achieved by altering the polymeric solution concentration. In the dilute and semi-dilute unentangled concentration domain droplets or beaded fibers are observed to form. Smooth uniform diameter fibers are observed to form at the onset of semi-dilute entangled concentration regime. For a given molecular weight, the increase in fiber diameter with increasing solution concentration is attributed to both the increase in the entanglement density and the decrease in the radius of gyration of solvated polymer molecules. Using this technique polymeric fiber arrays in single and multiple layers are demonstrated which can be used towards developing strong textiles, biological scaffolds, and sensor networks.